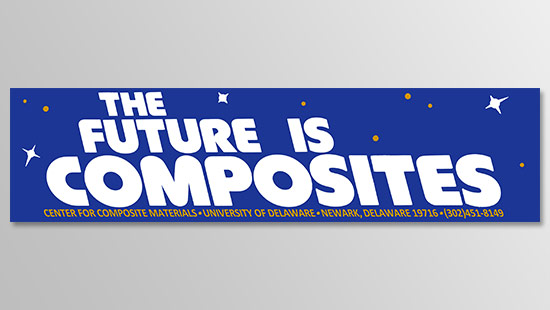
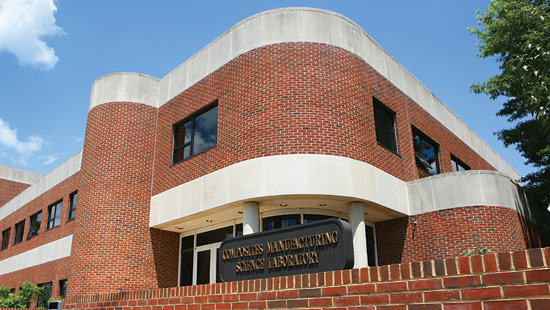
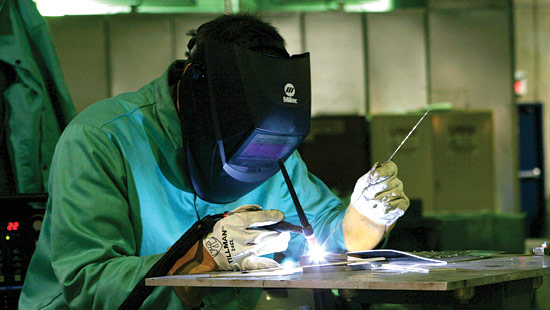
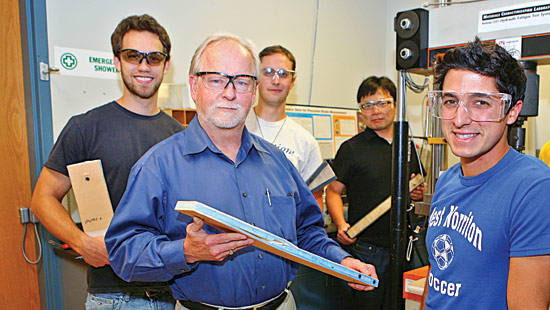
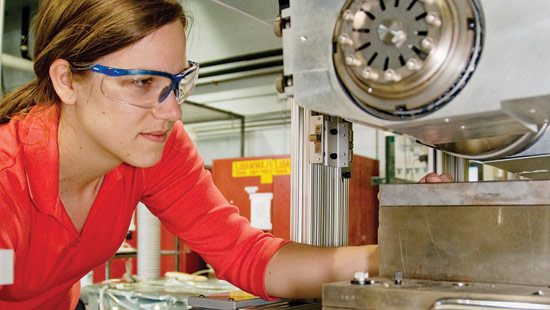
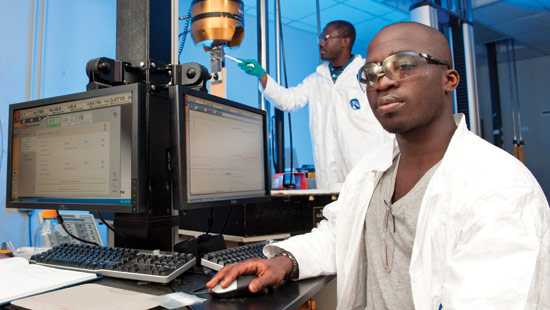
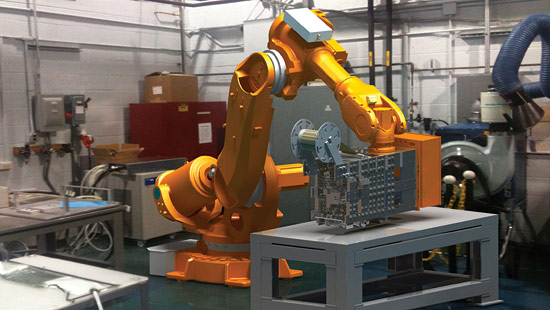
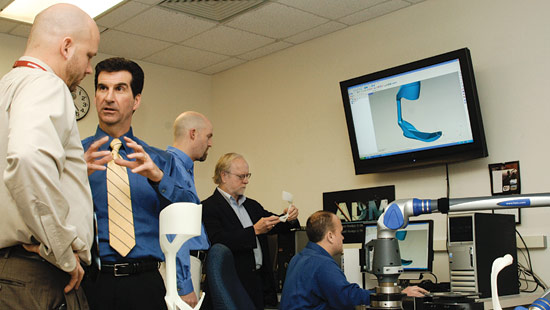
By diane kukichCollege of Health Sciences
A bumper sticker issued by the University of Delaware Center for Composite Materials in the 1970s proclaimed: "The future is composites." Center director Jack Gillespie, who was a UD graduate student at the time, believed that message then, and he still believes it today.
"What we're doing now is capitalizing on the traditional advantages of composites — they're strong, lightweight, corrosion resistant and tough — while infusing new functionality into these materials," says Gillespie, who is the Donald C. Phillips Professor of Civil and Environmental Engineering and also holds a faculty appointment in UD's Department of Materials Science and Engineering.
Polymers were first reinforced with fiberglass in the early 1940s. Since then, engineers across the globe have found thousands of ways to capitalize on the properties of composite materials, designing them into aircraft parts, boat hulls, pipes and tanks, car bodies, prefabricated bridge decks, bike frames, wind turbine blades and a variety of other applications.
But glass-reinforced polymers are just one example of a myriad of combinations that can be used to form advanced composites. Metals, ceramics, carbon and even natural substances are employed in these materials, whose properties are superior to those of the individual constituents.
Composites can be tailored to specific applications through the choice of an appro-priate combination of reinforcement, matrix material and manufacturing method — a fact driving both the benefit and the challenge of these "materials by design."
Referred to by a visiting committee member as "the top nationally and internationally recognized academic research center for composite materials," the Center for Composite Materials (CCM) at UD brings together a unique cadre of people and a state-of-the art assemblage of facilities and equipment to address composites design, analysis and processing.
More than 300 faculty, students, professionals and visiting researchers from industry and government agencies work together in CCM's two laboratories, which occupy a total of 52,000 square feet of space.
"Like the components of the materials themselves, our researchers work together to accomplish things that couldn't be accomplished by individuals," Gillespie says. "Composites are inherently multidisciplinary, and we have involvement from all branches of engineering as well as physics, chemistry and business."
With funding from the National Science Foundation and the Department of Defense (DoD), including in particular the Army Research Laboratory, CCM has been designated a Center of Excellence for 25 years. At the same time, the center has received strong support from industry through its consortium, "Application of Composite Materials to Industrial Products," which was established in 1978.
Although the center's industrial and government programs initially ran in parallel, over the years they developed a productive synergy and now are highly complementary, according to Gillespie.
"With our mix of people, we can cover the entire gamut from basic research to applied research to technology transfer. As we carry out fundamental research for our public-sector sponsors, we become involved with their private-sector contractors, enabling us to jointly transition technology into valuable applications," he says.
Others agree. Another visiting committee member commented after a program review that CCM's large multi-year government programs are relevant to many of the needs of the composites industry. "It is primarily because of the influx of government-sponsored work that the industrial program is so successful," he wrote.
CCM has been particularly successful in teaming with small businesses to win grants to transfer technology, accelerate commercialization and create new jobs in the state and nation. "We feel strongly that this is one of the most effective means to transition and commercialize technology," Gillespie says.
Just as CCM provides the framework for multidisciplinary research, composites provide the framework for the multi-functionality that is so hotly pursued in modern applications.
"Composites are an ideal lightweight host for a variety of functions, including communication, personal protection and sensing," Gillespie notes. "Because we design the material and the process at the same time, we can design in these new functions up front."
An approach known as multi-scale modeling, a high-tech term for being able to see the forest and the trees, is what enables all of these elements to come together in the right way at the right time.
"Many researchers today are investigating structures and materials at the nano-scale, but it's easy to get lost in that," says Gaurav Nilakantan, who earned his doctorate in materials science at UD in 2010 and is now a postdoctoral researcher at CCM. "As we explore things at the nano-level, we still have to keep an eye on the big picture."
Multi-scale modeling allows that perspective to be maintained by linking what is happening with a material at all scales.
As an example, Nilakantan points to research he is doing with Gillespie and Mike Keefe, associate professor of mechanical engineering, on the impact behavior of flexible textile composites. These materials are used in a variety of applications, including personal protective equipment such as bullet-proof vests and body armor.
"Common practice to qualify new materials requires testing of some 30 layers of fabric sandwiched together to see how the structure reacts to impact," Nilakantan explains. "But at the same time, we need to understand what's going on at smaller scales — with yarns, filaments, sub-filaments and even nanoparticles — so that we can improve the properties of the fabric, as all of those elements interact with each other.
"You can't look at anything in isolation," he adds, "because the entire structure needs to function in a certain way. A choice that optimizes strength, for example, might compromise the ability to embed sensors or communication devices."
Mark Mirotznik, associate professor of electrical and computer engineering, is working with Shridhar Yarlagadda, assistant director of research at CCM, and other center researchers to create the next generation of electromagnetically functionalized composite materials.
"By tailoring the electromagnetic properties of structural composites," Mirotznik says, "it may be possible to integrate antennas, electronics, frequency-selective surfaces, and other electromagnetic components into the structural skin of future commercial and military vehicles and structures." Funded primarily by the U.S. Navy and Army, the team is exploring new design methodologies and fabrication processes for producing structural composites with these unique properties.
While CCM has received strong support from the DoD and its industrial subcontractors, Gillespie emphasizes that the research conducted with this funding has benefits to all.
"Many of the technologies that we take for granted today grew out of war-time needs," he points out. "Military aircraft led the way for commercial aircraft, body armor for soldiers paved the path to protective clothing for prison guards and police officers, and armored vehicle technologies provided the foundation for automotive applications."
As an example of this at CCM, work done under the Advanced Materials Intelligent Processing Center (AMIPC), a program funded by the Office of Naval Research, resulted in significant advances in the understanding of material behavior and flow during liquid composite molding processes.
Led by Gillespie and Suresh Advani, George W. Laird Professor of Mechanical Engineering, the AMIPC resulted in the development of simulations that have helped reduce the cost of traditional trial-and-error molding and manufacturing practices for a broad range of applications, from car hoods to bridge decks — far beyond the Navy's interest in inserting composites into ship applications.
If the future is indeed composites, what does that future hold? Gillespie sees increasing exploitation of the system benefits of these complex materials. "This is where we can do better," he says. "We already know that composites are the best way to reduce weight without miniaturization. Now we just have to keep working on ways to increase the functional work that these lightweight but strong hosts can do."
The integrated structural composite fuel cell developed by Cedric Jacob and John Gangloff may someday help transform the world of renewable energy. For their innovative idea, the UD doctoral students in mechanical engineering won a $10,000 cash prize in the Owens Corning Composite App Challenge, a global competition to find new applications for composite materials. The duo plans to invest the winnings in future projects.
"When we do research here at the center," Gangloff said of UD's Center for Composite Materials, "we're trained to think about how what we're doing will impact government and industry, as well as how their needs and problems can provide direction for our work. The Composite App Challenge embodied that way of thinking, so it was the perfect outlet for our creativity."