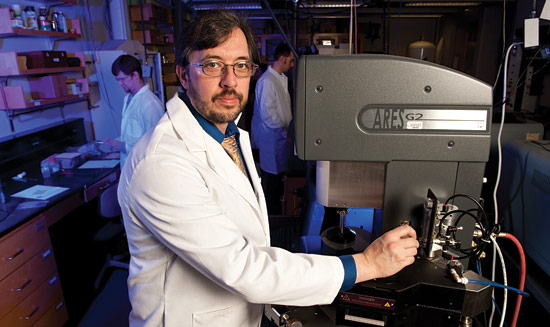
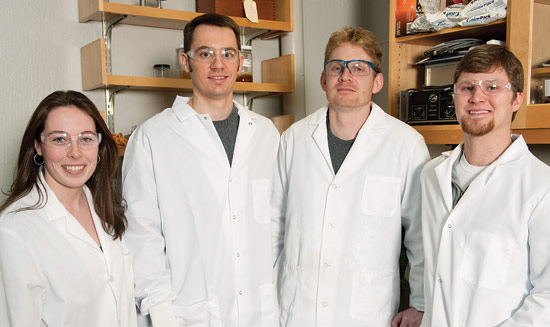
By tracey bryantOffice of Communications & Marketing
It's enough to make a superhero jealous.
Soft body armor treated with shear thickening fluid (STF), a novel technology invented by University of Delaware and U.S. Army Research Laboratory scientists, protects against practically any weapon the forces of evil can throw at it. It's bullet-resistant, stab-resistant, and can even protect the wearer from the shrapnel of detonated bombs.
Trademarked as Liquid Armor, the UD innovation is light and flexible —until hit by an object or shaken forcefully. Under this mechanical stress or "shear," the tiny particles of silica and polymers suspended in STF harden instantly, forming a protective shield. The hardening process occurs in milliseconds, and then the body armor becomes flexible again.
"The multi-threat protection is of particular value," says Norman Wagner, the Alvin B. and Julia O. Stiles Professor of Chemical Engineering and chairman of the Department of Chemical Engineering at UD. Wagner invented the STF technology in collaboration with Eric Wetzel, a scientist at the U.S. Army Research Laboratory.
"For first responders, you get not only ballistic protection with Liquid Armor, but you also gain this additional stab and puncture protection," Wagner notes. "And the material can do all of this while increasing the vest's wearability."
The police officer responding to a robbery, the prison guard making rounds, and the air marshal ever-vigilant on a domestic flight all come to mind as potential beneficiaries of the technology. And Wagner foresees many others someday, including doctors and nurses in the operating room, athletes in high-contact, concussion-prone sports, soldiers on the battlefield, even astronauts suiting up for a spacewalk.
Wagner is collaborating with the University's Office of Economic Innovation and Partnerships (OEIP), and with Barrday, UD's preferred partner on STF, to develop new applications and business opportunities.
"OEIP has been a fantastic partner — they've greatly supported these exciting development opportunities," Wagner says.
"One of the key features of this technology is that it can be customized based upon the threat and desired performance characteristics," notes Bradley Yops, interim director of the Technology Transfer Center within OEIP. "For example, you can optimize the STF formulation as well as the substrate fabric depending upon the level and type of protection desired, whether projectile resistance, stab or puncture resistance, or a combination of both."
Barrday, a specialty textile manufacturer with offices in Cambridge, Ontario, Canada, and Charlotte, North Carolina, makes textiles from aramid (aromatic polyamide) fibers, a class of strong synthetic materials that includes DuPont's Kevlar and Teijin Aramid's Twaron, as well as other fabrics that might comprise the base material for Liquid Armor. Barrday has set up manufacturing facilities to make the Liquid Armor for customers who will then take the material and transform it into products.
"Barrday has invested the time to learn what we do in the lab and to expand that process to a production scale. They are generating very high-quality Liquid Armor, which is critical in order for these materials to be certified as ballistic- and puncture-proof," Wagner says.
It's not easy working with STF, Wagner points out, because the material can rapidly become more viscous when subjected to mechanical stress, with the potential to damage processing equipment.
However, working out those kinks is worth it, Wagner points out, because Liquid Armor has a number of uniquely superior properties compared to existing body armor materials. It is thin and flexible, making it ideal for protecting the extremities — the arms and legs, Wagner says.
"We think there are a lot of opportunities to improve body armor, to create lighter, thinner, more wearable clothing while keeping the antiballistic strength intact. In making our material, we add STF to Kevlar or other fabric, but we need fewer layers to achieve the same result," he notes. "What we have to offer in Liquid Armor is a material that becomes a new tool in the toolkit of the armor designer."
Wagner's research lab resembles a scene from the movie Psycho when it comes to testing his favorite invention. The STF and fabrics treated with it are subjected to repeated knife stabs, not to mention hammering and dropped balls of varying weights and forces.
His research team is exploring the fundamental characteristics of STF using, among other tools, sophisticated rheometers that measure the flow of the STF in response to applied forces. Postdoctoral researcher Jeremy Fowler, recent doctoral graduate Dennis Kalman and doctoral student Kate Gurnon, and undergraduate students Paul Nenno, Tony Pallanta and Anne Golamatis work alongside textile engineer Kathy Zetune, formerly with ILC Dover, and research scientist Rich Dombrowski.
"What's cool is that we have an inter-disciplinary team that includes a textile engineer working with scientists, a postdoc, and graduate and undergraduate students in chemical engineering all involved in basic science technology development. Partnered with interested companies, we have formed a great product development team," Wagner notes.
Currently, Wagner's colleague Jack Gillespie, director of the Center for Composite Materials (see p. 8), and doctoral student Kate Gurnon are working to develop novel materials that could help increase the blast resistance of armored personnel carriers by keying on STF's unique combination of strength and damping ability.
The same principle is being explored in sports gear, from football helmets to hockey shin guards and shock-absorbent skis.
"Concussions are serious health issues," Wagner notes. "Shear thickening fluid has the potential to give a bit and absorb the shock waves so they don't damage the brain."
Currently, Wagner and his team are advising two design groups composed of UD seniors working on this promising usage.
Besides these down-to-earth applications, Wagner and his team also have a proposal under review by NASA for creating the next generation of spacesuits.
"Shear thickening fluid is not an easy technology to do," Wagner says. "It's like Edison showed us, it's easy to make a filament that glows, but harder to make the light bulb. However, it's an exciting technology to work with, and engineers like to tinker and invent things," he notes with a smile. "Good things will come out of it — it's just a matter of time and effort."
Liquid Armor is subject to a number of issued and pending domestic and international patent applications. For more information about Liquid Armor, contact Denise Bierlein, licensing analyst in UD's Office of Economic Innovation and Partnerships, at deniseb@udel.edu.
Fabric treated with shear thickening fluid (STF) undergoes a series of laboratory tests at the University of Delaware, including stabbings with an ice pick to assess puncture resistance. Above, the photos in the lefthand column show the puncture made in Kevlar. The righthand column shows Kevlar fabric treated with STF. It is fully intact, with no punctures.